I. The Exquisite Structure of Motorcycle Wheels
(I) Hub
- Materials and Types
- Motorcycle hubs mainly come in two materials: aluminum alloy and steel. Aluminum alloy hubs have the advantages of light weight, fast heat dissipation, and beautiful appearance. They are generally made by casting or forging processes. Cast aluminum alloy hubs have relatively low costs and high production efficiency, and can create complex shapes. Their weight is usually 30% – 50% lighter than steel hubs. A common 17-inch cast aluminum alloy hub weighs about 5 – 8 kilograms. Forged aluminum alloy hubs are stronger and more durable but also more expensive. Steel hubs are known for their sturdiness and low cost and are suitable for some heavy motorcycles or off-road motorcycles. In terms of strength, steel hubs can withstand greater impacts. Their yield strength can reach 300 – 500 MPa, while the yield strength of aluminum alloy hubs is generally 200 – 300 MPa.
- The hub structures include spoked and one-piece types. Spoked hubs connect the rim and the central hub through multiple metal spokes, which can better absorb vibrations and are suitable for driving on complex road conditions. The diameter of the spokes is generally between 3 – 6 millimeters, and the number is between 18 – 36. One-piece hubs are an integrated structure with high rigidity and are often used on high-performance motorcycles.
- Size Specifications
- Hub sizes are usually indicated by diameter and width. Common diameters are 16 inches, 17 inches, 18 inches, etc., and the width is between 2.15 inches – 4.25 inches. Different models and uses will choose different sizes of hubs. For example, sport motorcycles usually use hubs with larger diameters and narrower widths to improve handling and speed; while off-road motorcycles may use smaller diameters but wider hubs to enhance passability and stability.
(II) Rim
- Manufacturing Process and Material
- The manufacturing processes of rims include crimping, welding, etc. Generally, high-quality rims will use advanced welding technologies such as TIG welding to ensure the strength and flatness of the welds. Rim materials mainly include aluminum alloy and steel. After heat treatment and surface treatment, aluminum alloy rims have good corrosion resistance and appearance. Steel rims are more suitable for withstanding heavy loads and harsh environments. The surface is usually galvanized or chrome-plated to prevent rust.
- The shape and structure of the rim have an important influence on the installation and performance of tires. Common rims include deep-drop and flat-bottom types. Deep-drop rims are beneficial for tire fixation and sealing and are often used on high-performance motorcycle tires. Flat-bottom rims are more convenient for installing and removing tires and are widely used on some ordinary motorcycles.
- Safety Features
- The strength and safety of rims are crucial. Rims need to undergo strict tests, including radial fatigue tests and impact tests. In radial fatigue tests, rims must withstand a certain number of cycles of loads under simulated driving conditions. Generally, they are required to withstand 500,000 – 1 million cycles without damage. Impact tests simulate the impact force on the rim when the motorcycle encounters obstacles during driving to ensure that the rim can still maintain its structural integrity after being impacted to a certain extent.
(III) Connection between Tire and Hub
- Valve Structure and Function
- The valve is a key component for tire inflation and maintaining air pressure. Valves are generally made of metal or rubber. Metal valves are more durable, and rubber valves have better sealing performance. Inside the valve, there is a one-way valve that allows gas to enter the tire but prevents gas leakage. The thread specifications of valves usually include American and French types. American valves have thicker threads, and French valves have thinner threads. The length of the valve depends on the thickness of the hub and is generally between 30 – 50 millimeters.
- Installation Method and Fastening
- When installing a tire on a hub, special tools are needed to ensure a firm installation. The tire and hub are tightly fitted through the bead and the groove of the rim. During the installation process, evenly apply tire lubricant to facilitate installation and reduce the wear of the bead. After installation, use a tire wrench to tighten the tire bolts or nuts according to the specified torque. Generally, the torque of bolts is between 80 – 120 N·m, and the torque of nuts is between 60 – 90 N·m.
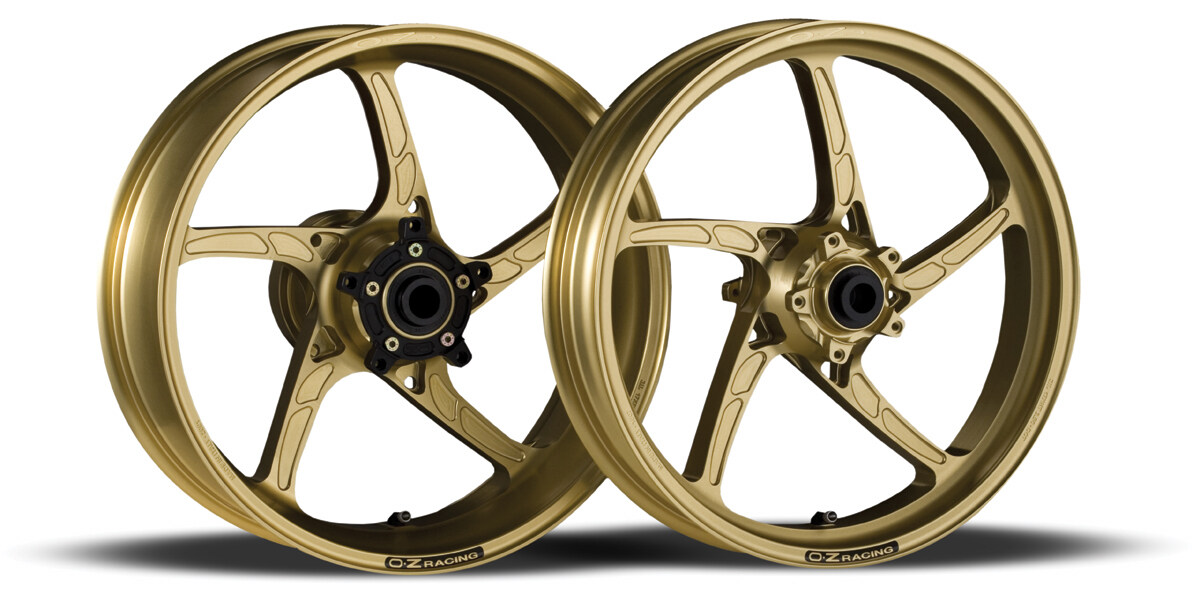
II. Working Principle of Motorcycle Wheels
(I) Support and Load Bearing
- Static and Dynamic Loads
- When the wheel is stationary, it has to bear the weight of the motorcycle itself, which is the static load. Depending on the type and weight of the motorcycle, the static load can range from several tens of kilograms to several hundred kilograms. During driving, the wheel also has to bear dynamic loads such as impact forces from the road, inertial forces during acceleration, and lateral forces during turning. For example, when a motorcycle is traveling at a speed of 60 km/h and brakes suddenly, the braking force on the wheel can reach 50% – 70% of the vehicle’s weight. The structure and material of the wheel must be able to withstand these loads to ensure driving safety.
- Load Distribution and Balance
- Whether the load on the wheel is evenly distributed has an important influence on the vehicle’s performance and tire wear. If the wheel is unbalanced, it will cause problems such as shaking and deviation during driving, and at the same time, it will accelerate tire wear. Generally, the dynamic balance error of the wheel should be controlled between 5 – 10 grams·meters. By adding balance weights to the hub, the balance state of the wheel can be adjusted.
(II) Rolling and Steering
- Rolling Friction Principle
- During the rolling process of the wheel, rolling friction is generated between the tire and the ground. The magnitude of rolling friction is related to factors such as tire pressure, tread pattern, and road condition. Appropriate tire pressure can reduce rolling resistance. Generally, the tire pressure of motorcycle tires is between 2.0 – 2.5 bar. The design of tire treads aims to provide good grip while minimizing rolling resistance. For example, the tread patterns of some highway tires adopt streamlined designs, and the rolling resistance coefficient can be as low as 0.01 – 0.02.
- Steering Mechanism
- When the rider turns the handlebar, the front wheel changes direction through the steering system. The steering angle and flexibility of the wheel are affected by multiple factors, including the structure of the hub, the design of the front fork, and the performance of the tire. During turning, the wheel needs to provide sufficient lateral force to maintain the stability of the vehicle. The cornering stiffness of the tire is an important factor affecting lateral force. The cornering stiffness is generally between 10 – 50 kN/rad, and the cornering stiffness of high-performance tires is usually higher.
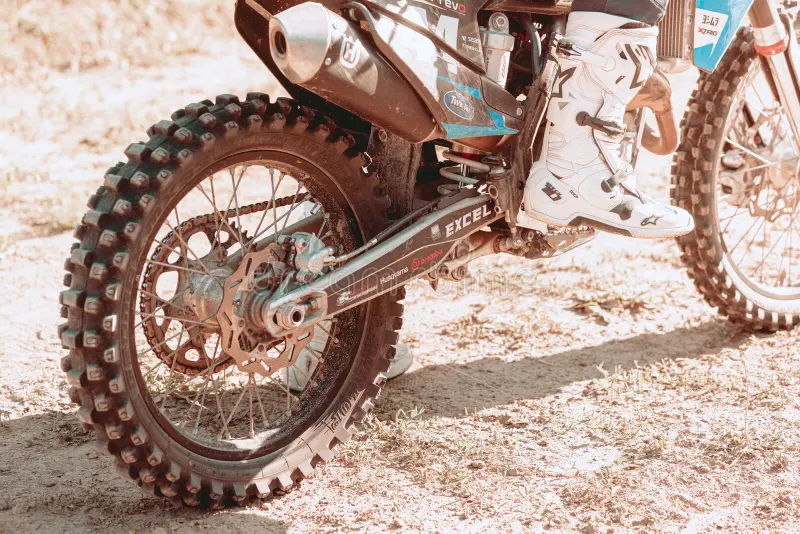
III. Maintenance Secrets of Motorcycle Wheels
(I) Daily Cleaning and Inspection
- Cleaning Frequency and Method
- It is recommended to clean the wheels at least once a week. Use mild car wash liquid and a soft brush to first clean the dirt, dust, and brake dust on the hub surface. For aluminum alloy hubs, special aluminum alloy cleaners can be used. Avoid using cleaners that are too acidic or alkaline to prevent damage to the coating on the hub surface. When cleaning the rim, pay attention to removing debris between the tire and the rim. After cleaning, dry the water with a clean towel to prevent rust.
- Before each ride, check whether the tire pressure is normal. Use a tire pressure gauge to measure and ensure that the pressure is in line with the value recommended by the vehicle manufacturer. Too high or too low tire pressure will affect the service life of the tire and the performance of the vehicle. For example, in summer high temperatures, the tire pressure may increase by 0.2 – 0.3 bar and needs to be deflated appropriately; in winter low temperatures, the pressure may decrease and needs to be inflated in time.
- Appearance Inspection Points
- Carefully check whether the hub surface has scratches, deformations, or cracks. For slight scratches, they can be gently sanded and then painted for repair; if deformation or cracks are found on the hub, stop using it immediately and replace the hub. At the same time, check whether there are signs of weld cracking at the welding points of the rim and whether the rim edge is worn or damaged.
(II) Regular Maintenance
- Dynamic Balance Inspection and Adjustment
- Conduct a wheel dynamic balance inspection every 5000 – 10,000 kilometers or every six months. Use a professional dynamic balancer to detect the imbalance of the wheel, and then add balance weights at appropriate positions on the edge of the hub. The weight of the balance weights is generally between 5 – 20 grams. Determine the quantity and position to be added according to the test results.
- Tire Rotation and Wear Inspection
- Rotate tires every 5000 – 8000 kilometers to ensure even tire wear. There are cross-rotation and parallel-rotation methods for front and rear tires. At the same time, regularly check the wear condition of the tires and observe the depth of the tire tread. When the remaining tire tread depth is 1.6 millimeters, the tire should be replaced in time. In addition, check whether there are abnormal conditions such as bulges and scratches on the side of the tire. If there are problems, the tire should be replaced immediately.
(III) Storage and Protection
- Precautions for Long-Term Storage
- If the motorcycle needs to be stored for a long time (more than one month), the vehicle should be parked in a dry and well-ventilated place. Use a motorcycle support stand to lift the vehicle so that the wheels are off the ground. Regularly check the tire pressure and keep it within the normal range. A layer of tire protectant can be applied to the tire surface to prevent rubber aging. At the same time, cover the motorcycle with a cover to avoid direct sunlight and dust erosion.
- Protective Measures
- During driving, try to avoid passing through sections with deep water to prevent water from entering the hub and brake system and affecting the wheel performance. If accidentally driving through muddy or sandy sections, clean the wheels in time after driving and check whether foreign objects have entered the brake system. When parking the vehicle, choose a flat ground to avoid the wheels being in an uneven stress state for a long time.
By deeply understanding the structure and principle of motorcycle wheels and strictly following the maintenance methods, we can ensure that motorcycle wheels are always in good condition and provide a safe and stable guarantee for our riding. Whether shuttling through urban streets or speeding on the racetrack, a wheel with excellent performance and proper maintenance is an indispensable key part of a motorcycle. Let’s take good care of motorcycle wheels and enjoy every riding journey.
The above is the relevant knowledge about motorcycle wheels. I hope it will be helpful to motorcycle enthusiasts.